What is the MTBF of a power supply unit?
MTBF stands for “Mean Time Between Failures,” and it is a measure of the average time that can be expected between the failures of a particular component or system. In the context of a PSU (Power Supply Unit), MTBF refers to the average time between failures of the power supply.
MTBF is often used to estimate the reliability of a component or system. It’s calculated based on data collected from real-world usage or testing. A higher MTBF value generally indicates a more reliable component, as it implies that the component is expected to operate without failure for a longer period of time.
The MTBF value is typically given in hours. For instance, a PSU with an MTBF of 100,000 hours would mean that, on average, the power supply is expected to operate for 100,000 hours before experiencing a failure.
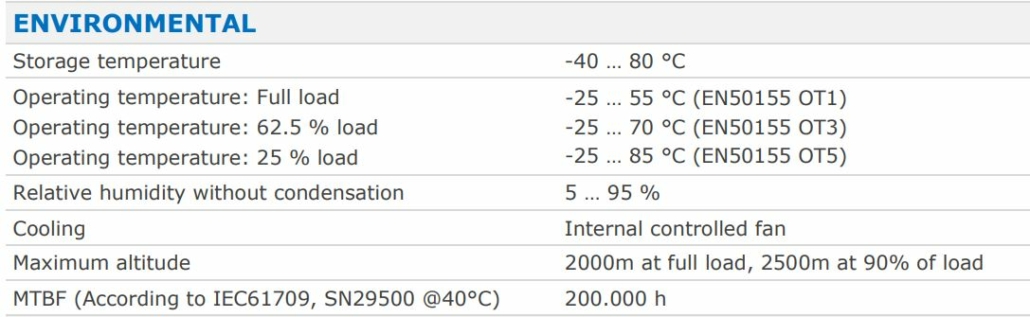
This is our CBS-10K’s datasheet with the parameter MTBF
It’s important to note that MTBF is a statistical measure and doesn’t guarantee that a particular component will last exactly that amount of time before failing. It’s a useful metric for comparing the expected reliability of different components or systems, but actual performance can vary due to a variety of factors including manufacturing quality, environmental conditions, usage patterns, and more.
How engineer’s department calculate the MTBF?
Engineers calculate the MTBF (Mean Time Between Failures) using historical failure data, reliability testing, and statistical analysis. Here’s a general overview of the process:
- Data Collection: To calculate MTBF, engineers gather data on the failures of the component or system over a period. This data could come from various sources, such as field data from deployed units, accelerated life testing, or reliability testing.
- Failure Count: The number of failures that occurred during the given time period is counted.
- Time Period: The total operating time of all units in the study is calculated. This could be measured in hours, cycles, or any relevant unit of time for the specific component.
- Calculation: MTBF is then calculated using the formula:
MTBF = Total Operating Time / Number of Failures
This gives the average time between failures for the studied units.
- Interpreting Results: The calculated MTBF value provides an estimate of the expected time between failures for a particular component or system. Engineers use this value to assess the reliability and make informed decisions about maintenance, replacement intervals, and design improvements.
It’s worth noting that MTBF calculations assume a constant failure rate, which might not accurately represent the real-world behavior of some components. Additionally, MTBF is just one aspect of reliability assessment. Engineers often use other measures like FALILURE RATE, MTTR (meant time to repair), or AVAILABILITY to gain a more comprehensive understanding of how a component or system behaves over time.
Furthermore, engineers might use specialized software or tools for reliability analysis that can help with more complex calculations and simulations, especially when dealing with intricate systems or large datasets.
Factors that affect the MTBF value and reliability
The MTBF (Mean Time Between Failures) of a device is influenced by various elements that collectively determine its reliability. These factors impact the average duration a device operates before experiencing a failure. Here are some key contributors to MTBF:
- Quality design: The stress of the components is crucial for the MTBF value. It is necessary to apply an appropriate safety margin to the components according to its maximum working conditions in voltage, current, power and temperature.
- Component Quality: The quality of individual components used in the device significantly influences its overall reliability. Higher-quality components are more resilient and less prone to failure, contributing to a longer MTBF.
- Environmental Conditions: The environment in which the device operates plays a critical role. Factors like temperature, vibrations, humidity, and dust levels can impact component performance and longevity. A controlled and clean environment typically leads to a longer MTBF.
- Usage Patterns: How a device is utilized affects its MTBF. Consistently running a device near its maximum capacity or subjecting it to heavy workloads can lead to higher stress levels and potentially shorter lifespan.
- Electromagnetic Interference (EMI) and Electromagnetic Compatibility (EMC): EMI can disrupt the operation of electronic components and lead to failures. Ensuring that components are shielded against EMI and that they meet EMC requirements is important.
- Maintenance Practices: Regular maintenance and servicing can extend a device’s lifespan. Neglecting maintenance or using improper servicing procedures might lead to premature failures, reducing the MTBF.
- Voltage Stability: Devices exposed to unstable power sources are more susceptible to failures. Voltage spikes, surges, or drops can stress components, affecting the overall MTBF.
- Operational Stress: Devices used in demanding applications, such as industrial machinery or data centers, might experience higher operational stress, impacting their MTBF compared to devices used in less demanding scenarios.
- Component Aging: Over time, components within the device can degrade. For instance, capacitors might lose their effectiveness, affecting the device’s overall reliability and MTBF.
- Redundancy and Design: Devices with redundant components or robust design features are often more resilient to failures. Such devices can have longer MTBF values due to their ability to continue functioning even if one component malfunctions.
Why is the MTBF important in power electric devices?
MTBF is important in power electronics devices for several reasons:
- Reliability Assessment: Power electronics devices, such as Power Supply Units (PSUs), inverters, converters, and voltage regulators, play a crucial role in various applications, including industrial machinery, telecommunications, consumer electronics, and more. Knowing the MTBF helps engineers and users assess the reliability of these devices, enabling them to make informed decisions about their deployment, maintenance schedules, and overall system reliability.
- Downtime and Cost: Failures in power electronics devices can lead to downtime in critical systems. Businesses and industries heavily rely on continuous operation, and any unplanned downtime can result in production losses, decreased efficiency, and increased costs. By understanding the MTBF, engineers can estimate the likelihood of failures and plan maintenance activities to minimize downtime.
- Design and Testing: Engineers use MTBF as a guideline during the design phase of power electronics devices. By aiming for higher MTBF values, designers can focus on incorporating higher quality components, better cooling systems, and robust designs that contribute to longer lifespans and improved reliability.
- Warranty and Customer Confidence: Manufacturers often provide warranty periods for their products based on their estimated reliability. MTBF plays a role in setting reasonable warranty periods, and customers can have more confidence in purchasing products that come with longer warranties based on higher MTBF values.
- Regulatory Requirements: In some industries, regulatory standards require that certain equipment meets specific reliability criteria. MTBF values may need to be demonstrated to comply with these standards.
- Predictive Maintenance: In larger systems or installations, such as data centers or power grids, tracking the MTBF of individual components can be valuable for implementing predictive maintenance strategies. By monitoring the operational status and estimated remaining life of components, maintenance activities can be scheduled before failures occur, minimizing disruptions.
- Total Cost of Ownership: When evaluating different power electronics devices for a project, considering the MTBF is important for calculating the total cost of ownership. A device with a higher MTBF might have a higher upfront cost but could lead to lower maintenance and replacement costs over time, making it a more cost-effective choice in the long run.
In summary, MTBF provides a valuable metric for assessing the reliability and durability of power electronics devices, helping engineers, manufacturers, and customers make informed decisions that impact system performance, downtime, maintenance strategies, and overall costs.